Bonnie Pankratz, President, AXIS Inspection Group Ltd.
NDT Methods
The most important question you need to ask when approaching Inspection and testing, is what do you want to accomplish? How does the inspection and testing that is done affect my bottom line and what information do you need for the application? This article is intended only as a basic introduction to guide and direct you to use the most efficient testing method for your project.
Surface methods
Visual Inspection, Magnetic Particle testing and Liquid Penetrant testing are considered surface testing methods; these methods assess the weld metal or parent material at a surface level. Visual Inspection is not just for welds, it is an important part of the quality overview for dimensioning, and general workmanship. Magnetic Particle Testing,(MT) has three types of test methods, which range in terms of sensitivity. How critical the area is and the surface type, will determine the appropriate method. Dry powder, Black on white (also called the wet method) and Fluorescent give increasing levels of sensitivity. It is important to mention that MT can only be performed on material that is magnetic, typically carbon steel. Magnetic Particle Testing is not suitable for aluminum or stainless steel applications.
Subsurface methods
Ultrasonic Testing (UT) and Radiographic testing (RT) are key testing methods in structural steel. These methods are important tools in structural steel. CSA S6[1] will require weld splices to be ultrasonically or radiographically tested.
Ultrasonic testing is commonly used as there are significant advantages of UT over RT in terms of cost efficiency. UT can be done during regular shifts, and as soon as Code allowances permit. [2] The technician is able to work alongside fabrication and mark deficiencies while fabrication is progressing. Two significant things to note, is that UT is only as good as the technician performing the work. The competency of the technician is an important factor in this method; secondly, there is no permanent record of the acceptable results.
Radiographic Testing is comprised of 2 methods, X-Ray and Gamma ray. Xray is limited as to the thickness of the material that it can test, so typically Gamma ray is the method used in Structural Steel. Gamma ray although provides a permanent record and is less subject in terms of the competency of the technician, the cost efficiency of the method is less attractive. Gamma Ray testing requires that the fabrication area and often the building be clear of non RT personnel. Often RT is performed during night shift which requires a cost premium to be paid, as well as preventing the option of a night shift for fabrication.
Phased array Ultrasound (PAUT) is becoming more widely accepted. This advanced NDT method combines that accessibility of Ultrasonic testing with the ability to provide a permanent printed record. CSA W59[3] has been recently revised to allow for the use of PAUT in structural steel applications. This method has some of the concerns of conventional UT, in that the competency of the technician is integral to the results. The qualifications and training is different than that of a conventional UT technician, which is an important factor when considering this NDT method for a project.
Material analysis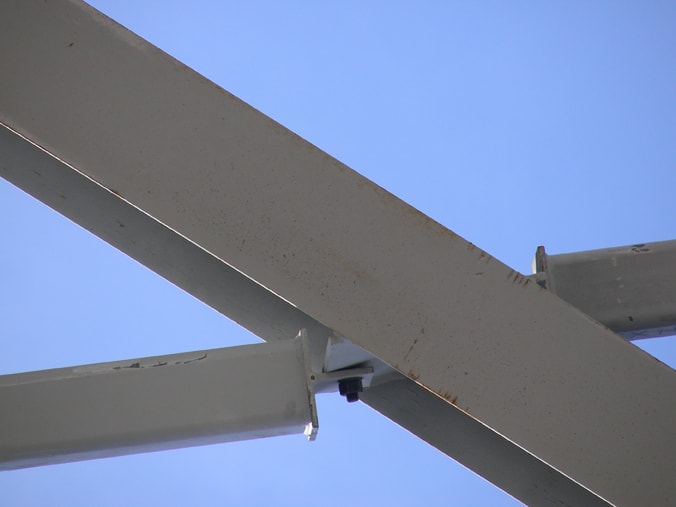
X-ray Fluorescence (XRF) this equipment is portable and analyses the chemical composition of a material. This method is key in ensuring that the material being used matches the properties of (Mill test report) MTR as to what has been specified as well as providing information when origin of material is unknown.
This is just a quick snap shot of NDT and not comprehensive or detailed. The primary purpose is to provide a launching place for the structural steel industry to have the knowledge to know to ask questions at the start of the project.
What information are you looking for when considering Quality Assurance, Quality Control, inspection and NDT? Send in your questions and we can continue this conversation.
[1] CSA S6 A10.1.8.2
[2] CSA S16 annex 19
[3] CSA W59 7.4.3.1