There is a new structural steel product form on the horizon. It can be manufactured in a condition as strong, tough, and corrosion resistant as a high strength low alloy (HSLA) steel. It can be custom produced in virtually an unlimited variety of shapes and in a wide variety of alloys. It will be manufactured by robots, and by its very nature it can be readily joined to existing product forms. What is it?
Wire Arc Additive Manufacturing
Wire arc additive manufacturing (WAAM) is an alternative to traditional metal manufacturing methods such as casting, rolling, forging, or the machining of raw billets to produce a desired shape. One option for this ‘3D-printing’ of metallic products is to use the common gas metal arc welding (GMAW) process delivered by a standard welding robot. (This combination is becoming known as GMAAM.)
While various methods for additive manufacturing, such as laser-based powdered fed processes, have been applied to relatively small-scale niche market products in the aerospace or medical sectors, the concept of using arc-based processes to produce large-format components from structural steel alloys is still relatively new. Much work needs to be done to develop a better understanding of the process variables, shape control, structural integrity, productivity rates, and the requirements for quality assurance and secondary processing before the structural steel engineering and design community will seriously consider the use of these components in their structures.
To help address some of these concerns Conestoga College in Cambridge, ON, has recently completed projects to produce a series of thin-walled plates with the WAAM process, where the thickness is less than 10% of the height, and destructively test the pieces using standard methods. [1, 2] These walls were created using common steel alloy feedstock (welding electrode) wires for structural steel work, including a nominal 1% nickel steel compatible with HSLA atmospheric corrosion resistant applications. The initial project phase was to develop a stable WAAM process and to produce a set of walls for testing, nominally 300 x 100 x 16 mm in size, as shown in Fig. 1.
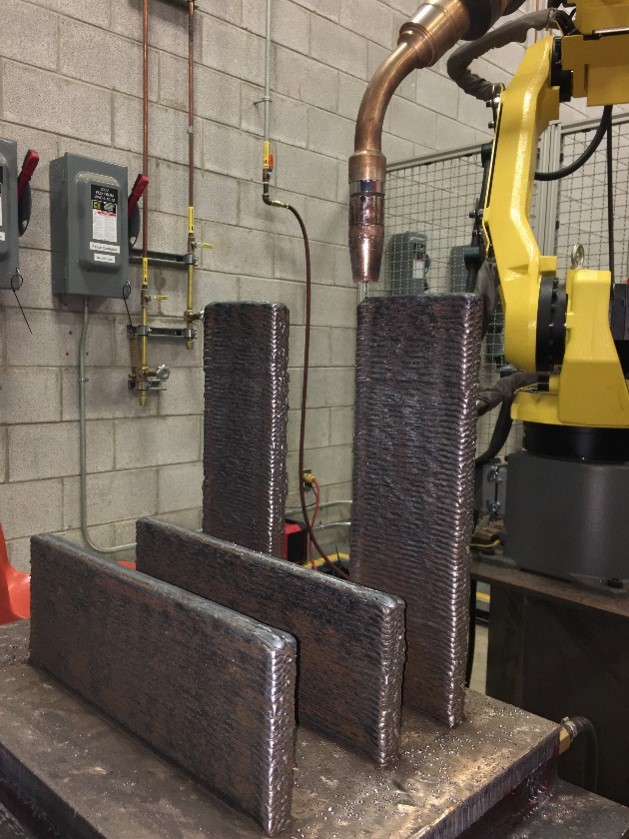
Figure 1:
Structural steel walls produced by the WAAM method at Conestoga for evaluation and destructive testing. Nominal size 300 x 100 x 16 mm
The follow-up phase studied the soundness and mechanical properties of the walls, which included tensile, hardness, impact toughness, and the general integrity (Fig. 2).

Figure 2:
Typical destructive tests conducted on the components.
WAAM Mechanical Properties and Material Soundness Results
Using the WAAM methods and materials in this study, mechanical properties exceeding the minimum requirements of standard grades of structural steel were achieved. The three feedstock wires used were common solid GMAW consumables conforming to CSA-W48 (ISO CAN/CSA-ISO 14341:11) and AWS A5.18M/A5.28M and requirements (ER49S-3, ER49S-6, and ER55S-Ni1). The following comparisons were made to CSA-G40.21:13 (R2018) [3]: ER49S-3 deposits to Grade 300WT Cat 2; ER49S-6 deposits to Grade 350WT Cat 4; ER55S-Ni1 deposits to Grade 400AT Cat 4.
Fig. 3 shows yield and ultimate tensile strength data from the tests that exceed the minimums required by the comparative steel grades.
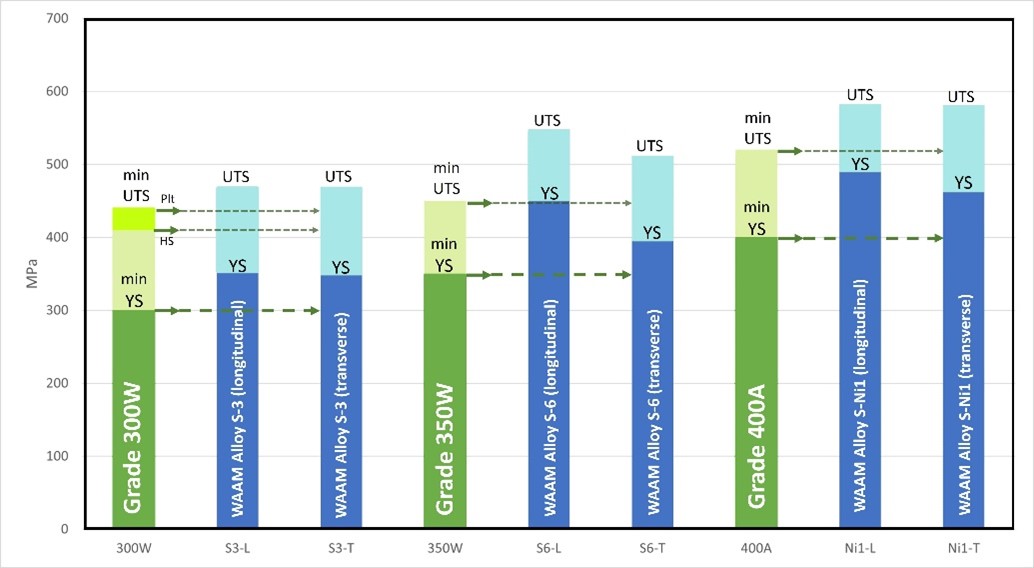
Figure 3: Results of tensile tests conducted both transverse and parallel (longitudinal) to the direction of the weld layering, in comparison to standard grades of steel (CSA-G40.21:13 (R2018) – Structural Quality Steel). The feedstock wires used were ER49S-3 (‘S-3’) – mild steel, ER49S-6 (‘S-6’) – mild steel, and ER55S-Ni1 (‘S-Ni1’) – 1% nickel HSLA.
The absorbed energy levels measured in Charpy V-notch (CVN) impact toughness tests far exceeded the 27 J minimum requirement at the comparative temperature, as shown in Fig. 4. The average Brinell hardness was 143, 190, and 199 (BHN) in the S-3, S-6, and S-Ni1 alloy blocks, respectively.
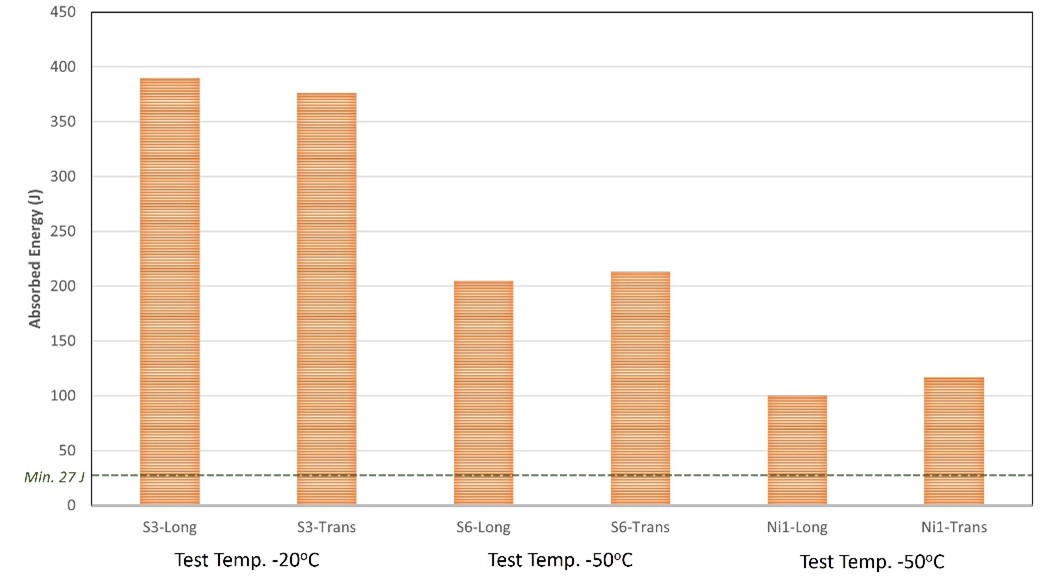
Figure 4:
Figure 4: Results of Charpy V-notch impact tests conducted both transverse and parallel (longitudinal) to the direction of the weld layering. The minimum absorbed energy requirement in CSA-G40.21:13 (R2018) – Structural Quality Steel, is 27 J (Test Temperatures – Cat. 2: -20oC; Cat. 4: -45oC). The feedstock wires used were ER49S-3 (‘S3’) – mild steel, ER49S-6 (‘S6’) – mild steel, and ER55S-Ni1 (‘SNi1’) – 1% nickel HSLA.
Dimensionally the walls were straight within 2 mm over the >300 mm length or width. The thickness of blocks varied from a minimum of 16 mm to a maximum of 21 mm at the sides where the welds initiate or terminate. The surface roughness (Ra) in the central portions was estimated to be ~300 μm.
A detailed optical examination of the microstructure of the WAAM walls showed a mixture of columnar (as deposited) and fine-grained reheated weld metal (Fig. 5).
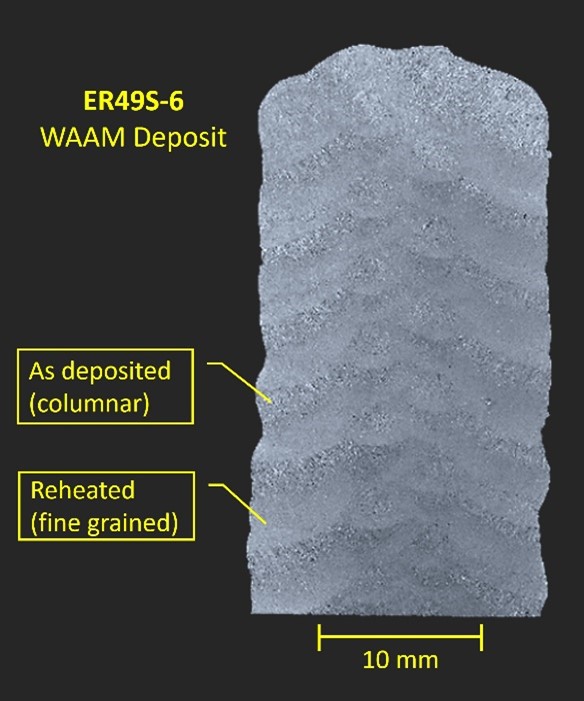
Figure 5:
Macrographic cross section of a typical WAAM deposit (near top). Etched in 2.5% Nital.
The relatively high absorbed energy values measured during low-temperature CVN testing is believed to be related to the repeated process of depositing weld metal (casting) followed by subsequent weld layering (reheating) and the resulting grain refinement. A high volume fraction of these fine-grained ferritic deposits are known to impart good toughness and strength in weld metal.
Extensive destructive testing for structural soundness of the products was performed to detect the presence of internal flaws, inclusions, or porosity. This included milling into the central layers, followed by fluorescent penetrant testing, and guided bend testing in several orientations. None of the guided bend tests on machined surfaces (e.g., side-bends, see Fig. 2) presented discontinuities exceeding the acceptance criteria in welding standards such as CSA-W47.1:19. [4] Other non-standard guided bend tests conducted on the unfinshed surfaces provided useful data, however there is presently no existing acceptance criteria to evalaute these tests. More details on these results are provided in a separate paper. [2]
Additional Qualification Work
Before any applications of WAAM components in steel structures can be considered, there is more work to do. Although industry has decades of experience with the alloys used in this study in weld joints, there are many variables that can influence the structural performance of the products produced by additive manufacturing that must be better understood. The quality of the WAAM products will be influenced by the chemistry of the feedstock wires, welding shielding gas composition, position and angles of layering with respect to gravity, welding parameters, heat input, technique (e.g., weaving verses stringer beads), and the inter-pass temperature. Ultimately it is anticipated that a fabricator would be required to qualify a procedure, or follow a prescribed prequalified method, in a similar manner to the current administration of welding procedure qualifications in CSA-W47.1:19. [4]
In addition, the service application may involve joints between WAAM components and conventionally manufactured materials, cyclic loading conditions, or corrosive environments. Concerns with residual stresses and distoration may arise. Fabricators will wish to minimize secondary operations and use the WAAM products in an as-welded condition without additional machining or grinding where aesthetics and service conditions allow this. Visual inpsection or other non-destructive testing will be specified to assure quality, and new acceptance criteria will be required.
Ongoing Work at Conestoga
With well established robotic welding and welding inspection capabilities, Conestoga is in a unique posisition to participate in this work. Since 2017 the projects in this field have involved a multi-disciplanary team of students and faculty from the Manufacturing Engineering Technology – Welding & Robotics; Welding Engineering Technology – Inpsection; and Mechanical Systems Engineering (MSE – B.Eng.) programs. In future work it is planned that students and faculty from the Structural Steel Management and Detailing and the Mechanical Systems Engineering – Joining and Welding Major Degree (MSE-JWM B.Eng. – under development) programs will also participate.
Ongoing work in this area involves employing offline programming software to develop layer slicing from 3-D CAD models and the creation of complex shapes. Students are working collaboratively using off-line programming software (OCTOPUZ®) with CAD to path capabilities.
The college is also seeking industrial partners to participate in and guide the applied research program development for applications in steel structures. Examples of concepts that are under consideration are illustrated in Fig. 6.
These include shape transitions (6a), complex connection nodes in tubular structures (6b), integral weld backing in components to avoid open root complete joint penetration (CJP) field welds (6c), decorative/structural members (6d), and even discrete components with variable alloy compositions and properties (6e).
Summary
The continued advancement of the WAAM process will open up new opportunities for structural steel architects and design engineers to explore ideas that were previously out of reach. It is anticipated that fabricators will find that automated WAAM production reduces supply chains, part inventories, and lead times. Field erection and welding operations will be simplified with tubular socket connections and intregral weld backing.
The path forward to acceptance and use of WAAM components in steel structures will require more than 3-D modelling and programming software. It will also be necessary to prove the structural integrity of large-format prototypes, determine essential variables and acceptance criteria, and establish a practical qualification framework.
Acknowledgements
The projects at Conestoga have already benefited from the expertise and efforts of over a dozen faculty and students. This work has been supported by Conestoga Applied Research – NSERC: Smart Manufacturing & Advanced Recycling (SMART) Centre (Technology Access Centre).
Author
Jim Galloway teaches Welding Engineering Technology at Conestoga College
References
- Vidal, et. Al, “Wire arc additive manufacturing with robotic GMAW”, Weld, Spring 2022.
- Galloway, “Investigation and qualification testing of GMAW wire arc additively manufactured structural steel components”, Weld, Spring 2022.
- Canadian Standards Association. 2018. “CSA-G40.21:13 (R2018) – Structural Quality Steel.” Toronto.
- Canadian Standards Association. 2019. “CSA-W47.1:19 – Certification of companies for fusion welding of steel.” Toronto.